Return to Construct Hokkaido(More articles in English here.)
Challenges facing builders of wooden structures – Wood shock creeping into Hokkaido Part 1
Drastically impacting the housing construction and lumber industries and causing price increases for detached houses.
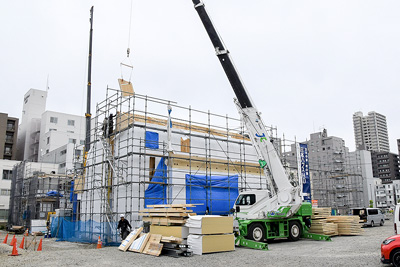
(construction site for a wooden structure in Sapporo)
A “wood shock” has been triggered by the rise in demand for lumber and housing in the United States and China, both of which have been severely impacted by the COVID-19 pandemic, as well as the do-it-yourself craze, thus resulting in soaring prices for foreign lumber and procurement difficulties. The impact of this has been significant, especially for housing companies. Here we will be examining what brought on this wood shock as well as talking with those on the front lines of Hokkaido companies who are struggling to deal with the situation at hand.
“The price per unit may have to be increased by approximately 2 to 3 million yen.” An employee of a medium-sized construction company in Sapporo that supplies housing built using foreign lumber was told by a lumber dealer that the price of foreign lumber delivered to construction sites between June and July would increase 1.2 times and that it would rise 1.5 times from August onward. The employee sighed, knowing that these cost hikes would have to be explained to customers in the future.
Lumber supply stability depends on the size of the company. Although one major house builder based in Tokyo seems to have secured enough foreign lumber for this year thanks to bulk purchasing by its head office, companies in Hokkaido find themselves stepping into a difficult situation. Johnson Homes Co., Ltd. (Headquarters: Sapporo) has begun to consider raising prices for some new houses in response to soaring lumber prices. One staff member said it would be difficult to maintain current prices due to surging land and building material prices.
The housing industry in Hokkaido has been recovering from the COVID-19 pandemic. According to the Ministry of Land, Infrastructure, Transport and Tourism, detached owner-occupied housing starts in 2020 totaled 11,090 units, down 6.9% from the previous year. Although housing starts declined due to the state of emergency that was declared in the spring of 2020, they have exceeded the previous year’s level since the beginning of this year. Housing starts for new detached houses for sale rose by 4.3% from the previous year to 2,707 units, showing an increase for the fifth consecutive year. Good locations and reasonable prices have been drawing in buyers.
However, as the wood shock became apparent, a dark cloud began to loom over housing construction. Ryuji Funahashi, Managing Director of the Association of Hokkaido House Urban Development, expressed his fears, saying, “Although we have enjoyed a booming market mainly in ready-built housing, our industry will be facing problems if purchase motivation diminishes due to the hike in housing prices.” Once prices rise, it can be difficult to return to the original price. To keep costs down, construction companies are forced to take measures such as narrowing plots and reducing the size of buildings, promoting new housing construction in the suburbs of Sapporo and strengthening ready-built house sales.
The wood shock has had no impact on construction firms that have traditionally used Hokkaido lumber. According to Tetsuya Takeuchi, president of Takeuchi Construction Co., Ltd. (Headquarters: Sapporo), “We have our own distribution route, so we don’t have to worry about running out of materials at the moment.” Naomi Yoshimura, president of Kinoshiro Taisetsu Co., Ltd. (Headquarters: Kuriyama), who also uses lumber from Hokkaido, views the trend positively, saying, “This is actually a great opportunity for consumers to look at homes made with Hokkaido lumber, which has up until now been seen as expensive.”
Although some expect Hokkaido lumber to serve as a substitute for foreign lumber, it won’t be easy. In addition to securing acquisition routes, there is currently no system in place to boost production capacity at sawmills, and most believe it will be impossible to make up for the decrease in foreign lumber.
Mitsuo Hasui, president of Iwakura Home Co., Ltd. (Headquarters: Sapporo) and director of the Hokkaido Branch of the Japan 2×4 Home Builders Association, says, “Even if many manufacturers temporarily look to domestic lumber, they will return to foreign lumber once prices and supply have settled down.” Furthermore, he suggested that Hokkaido lumber will not take root unless the housing industry continues to use stable amounts of it.
Houses can’t be built without procuring lumber. Market conditions are quite different from those of the past, and companies need to decide whether to secure distribution routes in new areas or wait for a stable supply of domestic lumber. Housing companies are being asked to use their management skills to survive in the industry.
(Excerpt from an article on June 10, 2021)
(This series was written by Takahiro Miyazaki and Riku Takada of the Economy and Industry Division and Miho Abe of the Obihiro Branch Office.)
メニュー